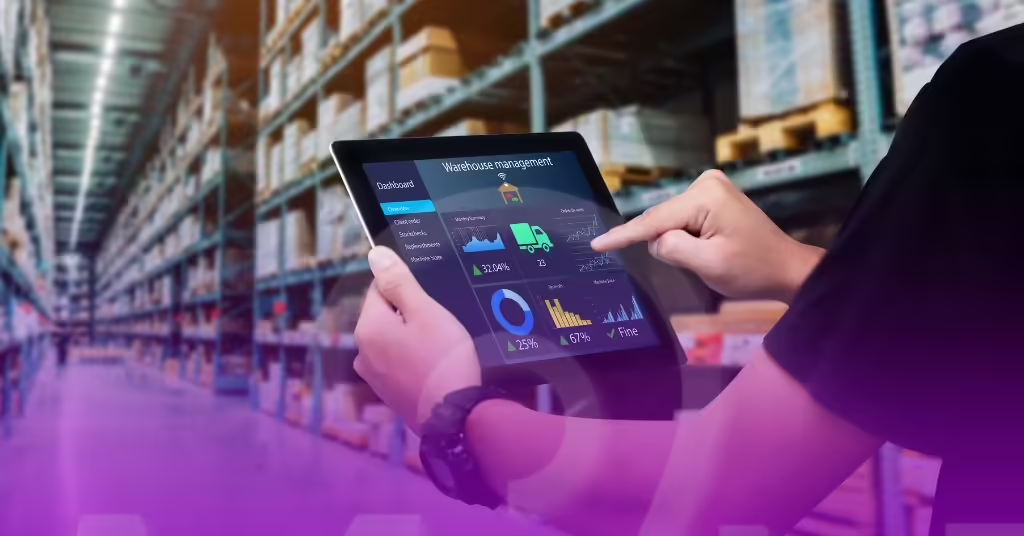
Warehouse Receiving Done Right: A Complete Guide to Key Processes And Best Practices
Warehouse receiving is the first step in the eCommerce order fulfillment process. When structured and streamlined well, a warehouse receiving workflow not only streamlines inventory management, it even makes fulfillment more cost-effective and efficient overall.
It’s also quite instrumental in preventing stock inconsistencies, ensuring accurate inventory counts, and avoiding delays in fulfilling orders. Any mistakes in this process can result in customer dissatisfaction and perhaps even order cancellation, not to mention loss in profitability and reputation. The following article discusses the key steps and best practices for an effective warehouse receiving process. Let’s get started!
Key Processes of Warehouse Receiving
The warehouse receiving process involves several key phases to ensure accuracy and timely handling of goods. Below is an overview of the important steps in the warehouse receiving workflow:
1. Pre-Receiving Documentation
Before placing an order or accepting goods, it’s essential to complete several pre-receiving tasks, the most critical of them being preparation of all necessary documents and their communication to the supplier. This minimizes confusion and ensures that goods arrive as expected.
When documenting your packaging and shipping requirements, make sure you mention the following:
- Labeling information
- Number of items per container or pallet
- Number of packages per pallet or items per carton
- Required size and weight
In many cases, a warehouse receiving order label is also used. This label contains a barcode that is attached to each stock item. The barcode allows for easy scanning and integration into the inventory and warehouse management software.
2. Unloading Goods
Once the shipment arrives, the next step is unloading the goods. Warehouse staff should be ready at the loading bay to receive the cargo from the delivery vehicle. To streamline the process, organize your unloading bays in such a way that items are loaded back-to-front, following the reverse order of the delivery schedule. This allows for quick access to the goods without needing to rearrange other shipments.
Depending on the size and weight of the shipment, different equipment, such as forklifts or pallet jacks, may also be necessary to unload the goods safely and efficiently. It’s equally important to train warehouse staff to handle the unloading process correctly to avoid mishandling or receiving the wrong items. If any issues arise, such as damaged goods or discrepancies, they should be resolved with the shipment provider before signing the delivery receipt.
3. Inventory Counting
After unloading the shipment, the goods must be counted to ensure that the received quantity matches the purchase order. Counting can be done manually for smaller shipments, but for larger deliveries, barcode scanning is often used to speed up the process and reduce errors. In case of any discrepancies in the quantity, these issues should be immediately communicated to the shipping provider for further action.
4. Goods Inspection
Alongside counting, it’s vital to inspect the goods for any damage or defects. Inspect the shipment for signs of tampering, broken seals, or damaged packaging. The product codes must also be verified to ensure they match the order. If damaged goods are found, they should be set aside and marked for return or replacement. Thorough inspection at this stage prevents faulty items from being stored or delivered to customers.
5. Data Entry and System Updates
When the goods have been counted and inspected, it’s time to update the warehouse management software with the received inventory. If you want to maintain accurate stock levels and make sure the inventory data is correct at all times, you cannot overlook this step. Real-time data entry allows for better tracking of goods and improves order fulfillment efficiency. Many warehouses integrate their warehouse management software with an order management system or an enterprise resource planning module, to ensure seamless updates across the entire supply chain.
6. Storage and Putaway
Organizing and Storing Goods
The final step of the warehouse receiving process is putting away the inventory in the correct storage locations. The goods are placed on shelves, pallets, or in bins, according to their type and size. You must have a storage system that allows for easy retrieval of goods during the pick and pack phases of order fulfillment.
Optimizing Storage
To optimize storage, heavier items must be placed on lower shelves and lighter items higher up. Fast-moving goods should be placed in easily accessible areas to minimize the time spent retrieving them. Proper storage has two benefits. Firstly, it ensures the efficient use of space, and secondly, it guarantees the safe storage and quick retrieval of goods.
Best Practices to Streamline Warehouse Receiving
An inefficient receiving process can slow down conversion cycles from raw materials to finished goods, increase order lead times, and ultimately lead to customer churn. Consider the following best practices to refine your warehouse receiving process to make it more efficient and error-free.
1. Invest in Warehouse Technology
Most of the tasks in a warehouse receiving workflow can be tedious and time-consuming when performed manually. Without automation, tracking inventory movement, labor availability, and product details can quickly translate into costly errors.
Implement an inventory and warehouse management software with a barcode scanner to automate routine manual tasks and optimize workflows. They also help you make better plans for inbound inventory, prevent overstocking, predict stockout situations and trigger replenishment orders. Some softwares also coordinate delivery schedules with suppliers and freight carriers to avoid congestion at the docks during peak times.
2. Track the Right Metrics
Sure, we must collect data at every touchpoint throughout the receiving process, but simply gathering information for the sake of it wouldn’t do much good. It is vital to also analyze this data to identify trends and root causes of inefficiencies.
Warehouse systems with built-in analytics capabilities can track important inventory metrics, such as:
- Dock-to-Stock Cycle Time: Measures how quickly items are moved from the receiving dock to storage.
- Inventory Levels: Tracks stock at various locations within the warehouse.
- Putaway Items Per Hour: Monitors the efficiency of placing items in storage.
- Average Storage Cost Per Unit: Assesses cost-effectiveness in storing products.
- Truck Turnaround Times at the Dock: Measures the efficiency of loading and unloading trucks.
3. Introduce a Well-Defined Labeling Structure
Nowadays, goodlabeling systems incorporate technologies like barcoding and RFID tags. This structure enables warehouse operators to update inventory details instantly as items are unloaded.
Having organized information about inventory allows for better insights into supplier performance regarding lead times, reliability, and product quality, and subsequently leads to improved decision-making.
4. Allocate Jobs to Labor Optimally
Labor costs usually represent a significant portion—ranging from 50% to 70%—of the warehouse operating budget. Efficient warehouse management softwares not just manage inventory, they even help prevent both under- and over-allocation of resources and balance workloads in a safe and sustainable manner.
5. Conduct Inspections Regularly
Regular inventory audits, including physical counts and cutoff analyses, are necessary for identifying inventory imbalances before they escalate into larger issues. These inspections can facilitate more accurate future warehouse receiving.
Integrated inventory management solutions assist with these audits by providing real-time updates on stock levels, damaged goods, and specific SKUs, simplifying inventory tracking.
6. Always Double-Check Documentation
It’s a no-brainer, but review the inventory received against purchase order documents thoroughly. Consider implementing a systematic approach to manage receiving and shipping documents. For example, you can assign numbers to each document type and label various forms in sequential order. This way, you can simplify the process and help staff identify any missing stock.
7. Train Your Staff
No matter how streamlined your processes are, there is always room for error. To avoid that, make sure your employees know each and every step in a warehouse receiving process, product codes, packaging requirements, etc. at the back of their hand. Distribute a detailed receiving manual outlining each process step with clear guidelines for inspecting, sorting, and verifying shipments to create a more efficient workflow. Conduct training sessions from time to time to make sure that new staff is up to speed with the latest inventory storage or quality control protocols as well as any changes in operational or technological processes.
Optimize Your Warehouse Receiving Process with Mile
Let’s be honest. We live in a world where technology drives business growth. So, regardless of whether you’re a B2B wholesaler or an e-commerce retailer managing orders from a warehouse, setting up a seamless and accurate warehouse receiving process must always be your top priority.
Mile supports businesses of all shapes and sizes in digitizing their warehouse receiving through integrated apps and APIs. It also offers a unified platform for managing inventory workflows, provides real-time visibility into warehouse operations, maps the receiving process, and generates labels for streamlined storage.
Furthermore, Mile’s warehouse management software enables tracking of inventory levels, boosts picking and packing accuracy through barcode scanning, and monitors shipments from dock to a customer’s door. It also offers intuitive reports and provides real-time insights and data from the warehouse floor as you restock inventory.
Schedule a demo today to discover how Mile can transform your warehouse receiving workflow.